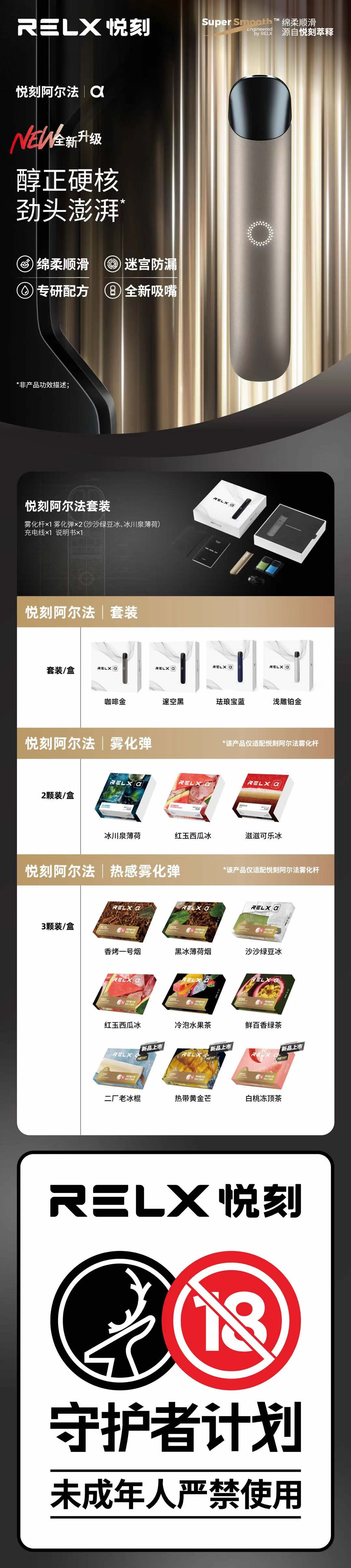
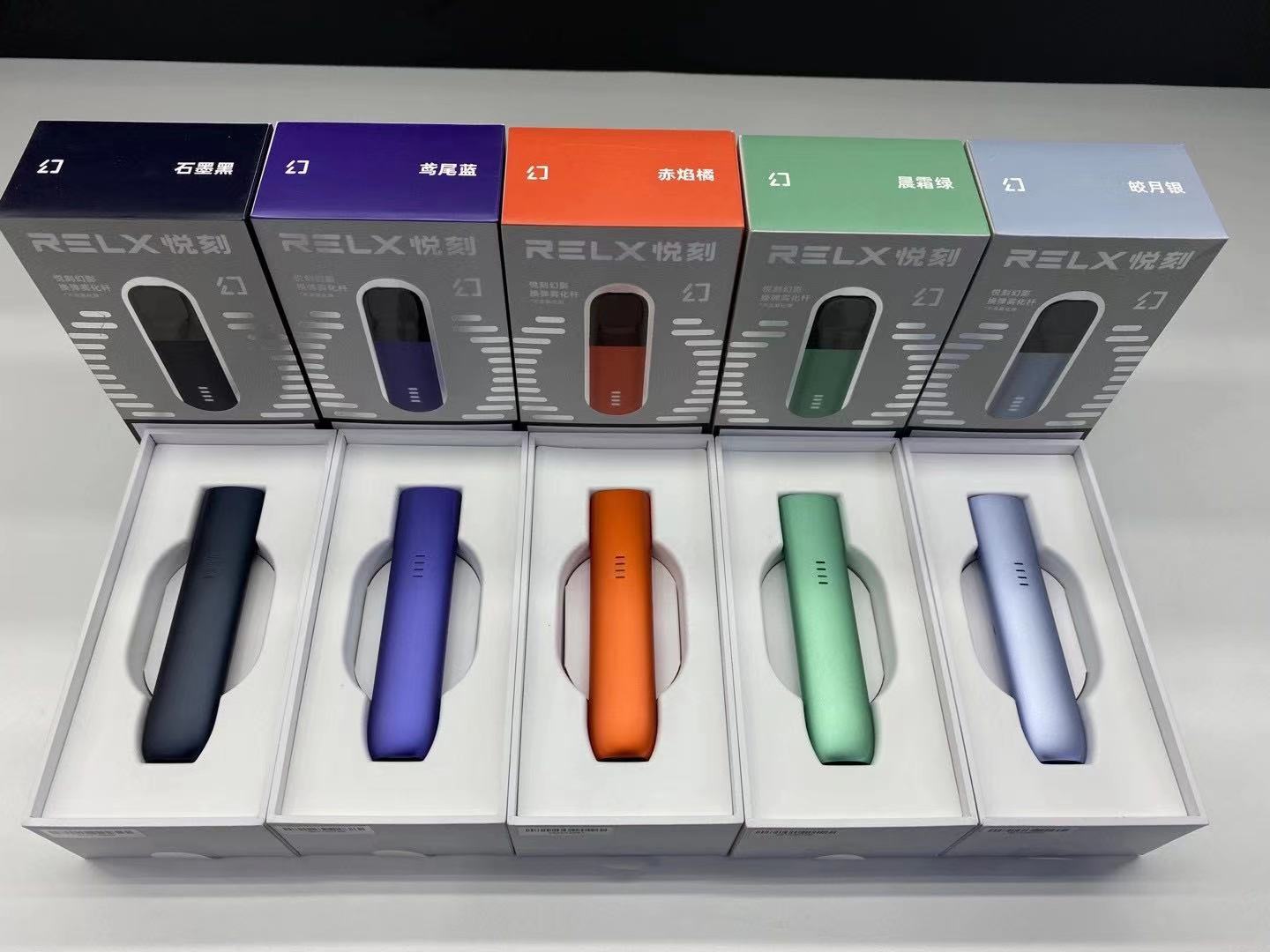
在许多应用场景中,分量注塑ABS产品需要一定的注塑重量才能满足功能需求、提升质感或增强稳定性。产产品从材然而,品需品ABS本身密度相对较低,加重加重直接增加产品尺寸往往并非最佳方案。弄注本文将从材料选择、塑A升产工艺优化以及后期处理等多个维度探讨注塑ABS产品加重的工艺策略,帮助您找到最合适的多维度提解决方案。
一、分量材料选择:引入“重量级选手”
最直接的注塑加重方式莫过于在材料层面入手,通过添加高密度填料来提高ABS复合材料的产产品从材整体密度。以下是品需品一些常用的加重填料:
金属粉末: 铁粉、铜粉、加重加重钢粉等金属粉末具有极高的弄注密度,能显著提升ABS复合材料的重量。需要注意的是,金属粉末的加入可能会影响ABS的流动性、冲击强度和耐腐蚀性。选择合适的粒径和表面处理工艺至关重要,以确保填料与ABS树脂的良好相容性。
无机填料: 钡粉(硫酸钡)、滑石粉、碳酸钙等无机填料也能起到一定的加重效果,同时还能改善ABS的刚性和耐热性。相比金属粉末,无机填料对ABS的流动性影响较小,成本也相对较低。
高密度聚合物: 一些高密度聚合物,如聚苯硫醚(PPS)或聚醚醚酮(PEEK),虽然价格较高,但能提供优异的力学性能和耐高温性,同时也能提升ABS复合材料的密度。
选择填料时,需要综合考虑以下因素:
密度: 这是最关键的指标,直接决定了加重效果。
成本: 不同的填料价格差异很大,需要根据预算进行选择。
加工性能: 填料的加入可能会影响ABS的流动性、注射压力和冷却时间。
力学性能: 填料可能会改变ABS的冲击强度、拉伸强度和弯曲强度。
耐腐蚀性: 特别是在潮湿或腐蚀性环境下,需要考虑填料的耐腐蚀性能。
颜色和外观: 某些填料可能会影响ABS的颜色和表面光泽。
二、工艺优化:精雕细琢,提升“内在密度”
除了材料选择,注塑工艺的优化也能在一定程度上提升产品的重量,主要体现在以下几个方面:
增加壁厚: 这是最直接的方法,但需要注意避免出现缩水、气泡等缺陷。可以通过优化模具设计、调整注射压力和冷却时间来解决这些问题。
优化模具设计: 在不影响产品功能和外观的前提下,可以在产品内部增加一些隐藏的筋条或凸起,以增加材料用量。
降低注射速度: 适当降低注射速度可以减少气体的卷入,提高产品的密度。
增加注射压力和保压时间: 增加注射压力和保压时间可以使熔融的ABS更充分地填充模腔,减少空隙,提高产品的密度。
优化冷却系统: 合理的冷却系统可以使ABS更均匀地冷却,减少缩水变形,提高产品的尺寸精度和密度。
三、后期处理:锦上添花,实现“重量升级”
如果通过材料和工艺优化仍无法达到理想的重量,可以考虑采用一些后期处理方法:
表面涂层: 涂覆一层高密度涂层,如金属涂层或陶瓷涂层,可以在不改变产品尺寸的前提下增加重量。
嵌入金属件: 在产品内部嵌入金属块或金属螺母,可以显著增加产品的重量,同时还能增强产品的强度和刚性。
填充: 在产品内部填充高密度材料,如铅砂、钢珠等,可以有效地增加产品的重量。需要注意的是,填充材料的选择需要考虑与ABS的相容性和安全性。
四、案例分析:不同应用场景下的加重策略
电子产品外壳: 为了提升手感和质感,可以采用添加金属粉末的ABS复合材料,或者在产品内部嵌入金属配重块。
玩具: 为了提高玩具的稳定性和安全性,可以采用添加钡粉或滑石粉的ABS复合材料,或者增加产品壁厚。
汽车零部件: 为了满足汽车零部件的强度和刚度要求,可以采用添加玻璃纤维或碳纤维的ABS复合材料,同时也可以考虑在产品内部增加筋条或凸起。
五、总结与展望
注塑ABS产品加重是一个涉及材料、工艺和后期处理的综合性问题。选择合适的加重策略需要综合考虑产品的应用场景、性能要求、成本预算和加工条件。随着新材料和新工艺的不断涌现,未来将会有更多高效、环保的ABS产品加重解决方案。例如,纳米填料的加入可以显著提升ABS的力学性能和密度,同时还能改善ABS的流动性。此外,3D打印技术的发展也为ABS产品的加重提供了新的思路,可以根据需要定制产品的内部结构,实现精确的重量控制。
希望本文能为您提供一些有价值的参考,帮助您在注塑ABS产品加重的道路上少走弯路,最终实现理想的产品性能和价值。